By Jay Palter | August 10, 2021
Equipment management is an afterthought at some companies. But those companies are usually surprised when they get around to adding up the costs of their equipment losses and operating inefficiencies. Better equipment tracking can eliminate those inefficiencies, reduce losses, and extend the lifecycles of each piece of your company’s equipment.
We have some thoughts on how you can best do all three. In this article, we’ll investigate the benefits of automating equipment tracking and offer six tips any company can use to improve their tracking.
The Benefits of Equipment Inventory Tracking
Automating equipment and inventory tracking using an electronic system can offer a broad range of benefits, including:
They allow for detailed data collection.
Electronic inventory tracking systems can log a much finer level of detail than a manual, pen-and-paper process ever could. In addition, many modern tracking systems use wireless tag and sensor networks, so each piece of equipment becomes “location-aware.” That means inventory items can collect live information about where they are and how your staff uses them around your facility.
Sensors transmit that detailed usage data to the tracking system’s central management dashboard. There, you can run reports to find out whatever you need about equipment usage.
Previously, only large enterprises had the budget to afford this type of Internet of Things (IoT) sensor technology. But advances in recent years now put this technology within the financial reach of SMBs.
They can improve employee accountability.
An automated tracking system can make your employees more accountable for their equipment use. The detailed logging provided by an automated system allows you to check in real time who has signed out which devices from your storage system and when they are due to return their equipment.
You can also set curfews in the tracking system for sensitive equipment sign-outs. The curfews trigger alerts to supervisors if equipment isn’t returned on time. If your company is bound by any equipment tracking regulatory standards, this capability makes an automated tracking solution an excellent tool to maintain compliance.
They can decrease costs and improve efficiency.
An inventory tracking system streamlines a process that is often error-prone and labor-intensive when performed manually. In addition, automating the tedious work of logging transactions, notifying staff of overdue returns, and tracking reservations free up your team to take on revenue-generating activities.
For example, you can use an automated system to rotate which laptops are available for sign-out so that wear and tear is evenly distributed across your entire inventory. Staff can’t have a favorite device that they sign out repeatedly, accumulating software glitches and physical damage.
They can prevent loss.
Sign-out curfews are also an excellent tool for reducing equipment losses. Supervisors can also set alerts to trigger if staff members haven’t returned any equipment at the end of a shift or within a custom time frame. You’ll be able to initiate searches as soon as possible, which many companies have found significantly increases their chance of equipment recovery.
6 Equipment Tracking Tips Any Company Can Use
As you can see, electronic asset tracking systems are fantastic tools. But an effective tracking program requires more than technology. Here are six things we think your organization should do if it wants to improve all aspects of its corporate equipment tracking, both with and without an automated system:
1. Perform an inventory audit.
Before you make any changes to your inventory tracking process, you should first conduct a top-to-bottom audit of everything your company currently owns. An audit is a crucial first step in any business sector, especially those using advanced, networked IoT technology. A single rogue IoT device can be the gateway a hacker is looking for to compromise your corporate network.
Every process change you make down the line will be more effective if you start with a complete audit up front. You’ll want to track all relevant information, including at least:
- Equipment owner
- Make
- Model
- Serial number
- Warranty information
- Purchase date
- Lifecycle end date
Keep this inventory up to date by scheduling periodic reviews. Reviews can be annual, quarterly, or at another interval you determine based on your risk profile.
2. Create an equipment inventory policy.
Once you’ve produced a reliable inventory and established a review schedule, the next thing to do is to set an equipment management policy. Be transparent in this process. Outline every critical role and responsibility, and define all of your essential equipment management best practices.
Your best practices should cover responsibilities during both routine operations and emergencies. You should also lay out all essential inventory management procedures. As we like to say, you want to track your equipment “from the cradle to the grave.”
You’ll want to establish procedures for equipment purchasing and intake. Any new equipment coming into your organization will need to be logged and tagged into your management system. Electronic devices, such as laptops, smartphones, and tablets, will need to be provisioned with your company’s security software.
3. Track damage and loss.
You’ll also want to define a procedure for what employees should do when they report equipment lost, stolen, or damaged. If not adequately managed, equipment loss can severely eat away at your equipment budgets. Loss tracking is also frequently mandated by different industry regulations, such as healthcare or the energy sector.
Link any loss reporting forms that employees will need in your policy document to be readily available. Monitor your tracking logs for noteworthy trends.
For example, when looking at maintenance records, does one of three different handheld scanner models account for three-quarters of all maintenance requests? If so, you might drop that model from your next inventory refresh.
4. Track usage.
Tracking exceptional events such as damage and loss is vital, but you’ll still want to track day-to-day usage. Why? The analytics software in an equipment tracking system can uncover trends you might not have noticed in the course of daily operations.
For example, do you have one employee who is regularly late returning equipment, impacting others’ use? Is one shift responsible for a high percentage of all equipment damage or loss? Once you see these events in your tracking data, you’ll be able to investigate and uncover underlying performance or potential shrinkage issues.
5. Track and schedule maintenance.
You will also want to track the maintenance schedules and warranties for your inventory. Ensuring you keep to all maintenance schedules will help you extend equipment life cycles.
An automated equipment tracking system will also help you keep tabs on your warranties. You can set the system to send you alerts when they’re close to expiring. For critical equipment, you can even tell the tracking system to lock those devices down to prevent them from signing out.
6. Use cost-effective tracking tags.
Consider using an automated asset tracking system that can automate all of the time-consuming work that comes with managing equipment. These systems can use various access control tools to manage who can sign out stored equipment.
Take the time to select a tag type that is both cost-effective and appropriate for your security and management needs. Two of the most popular tag types include:
Barcodes
Budget-conscious businesses often opt to use barcode scanners at their storage lockers. These scanners are good for basic, low-cost tracking. However, barcode labels can wear off over time, and their tracking capability is limited to logging at the transaction point.
RFID
Radiofrequency identification (RFID) is a short-range wireless standard that provides more tracking capabilities. You can attach or embed RFID tags to your equipment. Sensors connected to your equipment tracking system record the location of those tags as they pass nearby.
You can place those sensors at your storage locker and throughout your facility, if you want real-time tracking for equipment in use. You can also add sensors inside your storage locker compartments, which is called content surveillance. Content surveillance helps you verify whether staff members return the correct piece of equipment when they log a return for added accountability.
RFID tags are more expensive than barcode labels, but they’re also much more durable, so much so that many providers will offer a lifetime warranty on their RFID tags.
RFID tags also make transactions more efficient. You can scan multiple tags simultaneously, such as individually tagged components within a kit. In some settings, RFID tags may be the only viable option, especially if tagged equipment needs to be cleaned or sterilized, as is often the case in healthcare.
Equipment Tracking: A Core Component of Physical Security and Management Programs
An equipment tracking solution can be an excellent addition to any company’s security program. It can improve device security and improve your team’s overall performance. But powerful technology like that works best when combined with equipment management policies, inventory auditing, maintenance schedules, and other best practices.
Do you want to learn other ways you can improve your inventory management? Then check out our guide, Best Practices for Physical Asset Management.
Subscribe to our blog
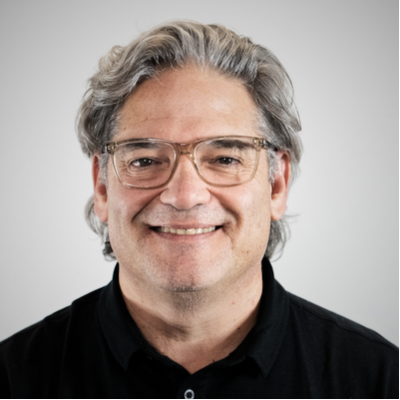
Jay Palter
Vice President of Marketing & Partnerships