Are you in the UK? Then we have a UK-specific article on avoidable workplace safety problems just for you.
Right now, many companies across North America and the UK have made it a priority to update their workplace safety plans. Some companies have access to COVID-related funding to improve workplace safety, others are reorganizing their strategy to accommodate hybrid workforces, or others are simply moving into new facilities.
Whenever you update something as critical as a workplace safety plan, you risk overlooking important details. No matter how thorough you think you’ve been, when you’re designing something as complex as a safety plan, small but important details will inevitably slip through the cracks.
You don’t want first to discover you’ve missed one of those essential details in the middle of an emergency. Extensive training and drilling are the best way to prevent that from happening. So is studying some of the critical problems other companies have encountered.
This article will first provide context for determining your company’s priorities when formulating your workplace safety program. Then, to help you make your planning go smoothly, we’ll go over eight workplace safety problems we’ve seen many businesses forget to address.
Set Your Priorities Before Disaster Strikes
During a workplace emergency, first and foremost, you’re responsible for the safety of your personnel and the surrounding public. But your responsibility doesn’t end there. You’re also responsible for protecting the financial future of your company.
Proper workplace safety planning takes an investment in time up front. Businesses should treat this type of planning as a strategic priority. Federal studies have consistently found that every $1 invested in emergency planning can prevent up to $4 in future losses.
A solid workplace safety plan will help you set clear priorities, protect your people, and protect your business assets should disaster strike. In North America and the United Kingdom, governments at the national and local levels mandate many different levels of emergency preparedness. The primary national-level regulatory bodies in these countries are:
- The Occupational Health & Safety Administration (OSHA) in the United States
- The Canadian Centre for Occupational Health and Safety (CCOHS) in Canada
- The Health & Safety Executive (HSE) in the United Kingdom
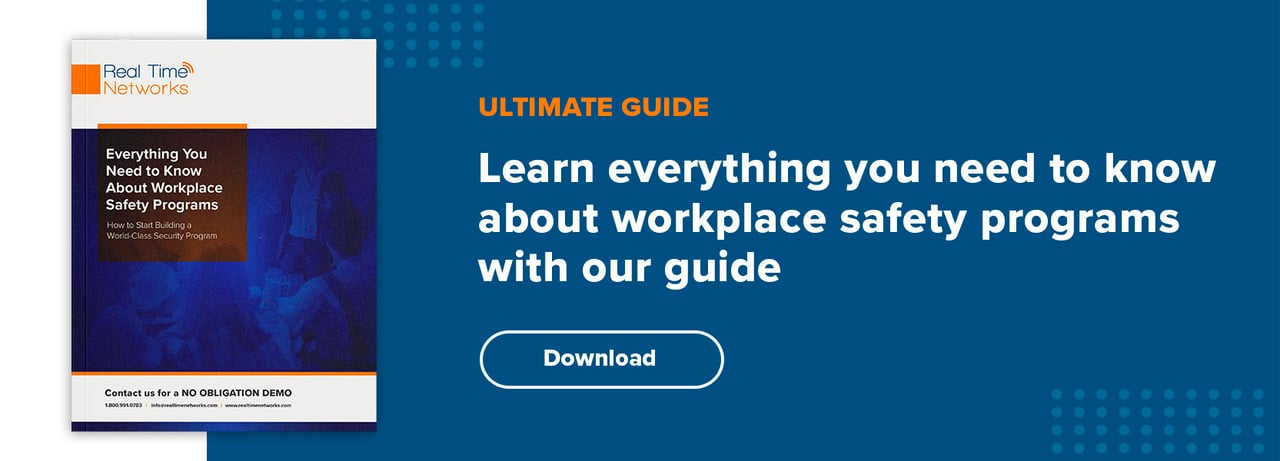
8 Workplace Safety Problems You Can Avoid
Most companies can meet their workplace safety obligations by performing a basic risk assessment and instituting a few essential safety precautions and evacuation plans. Only in specific higher-risk sectors will more complicated planning become necessary.
Here are eight problems you’ll want to avoid if you’re designing a new workplace safety program. Taking the time upfront to address these and other common issues will ensure your employees and your business are protected for years to come.
1. Not documenting an Emergency Action Plan (EAP) 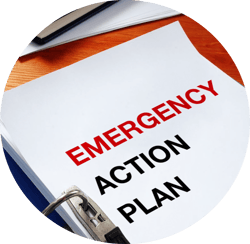
An emergency action plan is a unifying document that outlines all of the essential roles, responsibilities, and actions that must take place during a workplace emergency. Make a point to generate this document as you go about updating your safety procedures, don’t wait until after to assign someone to write it.
Some roles you might want to set out in your EAP include:
- An emergency manager who will be responsible for coordinating with emergency service teams on site
- First aid providers for each group or each muster point where workers will evacuate
- Essential personnel who will shut down critical business systems before they evacuate
As for procedures, your EAP should detail every shutdown procedure for critical business systems. Of course, you’ll want to have those essential personnel trained in these procedures, but if they are incapacitated or unable to reach those systems during an emergency, other personnel on hand should be able to reference your EAP to complete the procedure in their place.
The last thing your EAP should detail are the evacuation routes out of your facility and the muster points—sometimes called assembly points—where your personnel will gather for roll call, first aid, and other recovery activities.
For more emergency preparedness tips, please see our Complete Checklist for Emergency Preparedness in the Workplace.
2. Not coordinating your plan with emergency services
Resolving workplace emergencies takes careful coordination with emergency services. That coordination needs to begin long before an emergency is declared. Start by including representatives from local law enforcement, fire, and emergency medical services in your planning process.These representatives can provide valuable input on where best to evacuate, what considerations you should make for the local environment, and even what emergency events you’ll want to prioritize. In addition, they will know best what you might have overlooked or what additional steps they want you to take to ensure staff safety.
If you’re located in a business park or a multi-tenant building, you might also want to include neighbouring companies in your planning process. When you’re close, emergencies are likely to affect you together. You may also be able to share emergency management duties and coordinate your muster points.
3. Only thinking about business hours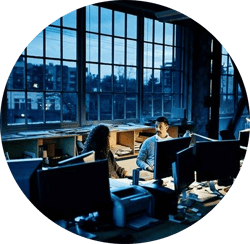
When developing your workplace safety plan, you also need to consider the safety of people in your facility around the clock, including nights, weekends, and holidays. In your EAP, define roles, responsibilities, and procedures for protecting second and third shift workers as well as anyone who must be in on weekends or holidays, like security and cleaning crews.
The procedures you design for these times may need to be very different, as you likely will have a much smaller number of people on site. While that will make it easier to evacuate, you’ll have fewer individuals available for your different emergency response roles.
4. Evacuating without emergency managers
Before your next evacuation drill or training session, assign responsible employees to be emergency managers for each floor or department in your company. The exact number you need depends on the size and complexity of your facility.
Emergency managers ensure that the other employees in their assigned area evacuate orderly and efficiently. You could also set your emergency managers essential closedown duties, such as closing firebreak doors or shutting off critical systems.
5. Forgetting about employees who need assistance
Your workplace safety plan must also include measures for protecting individuals who need assistance when evacuating your facility. Depending on your facility layout, you might need to have procedures for assisting:
- Children on-premise or parents with infants
- Elderly, ill, or disabled individuals
- Isolated workers
- Individuals working near fire ignition sources or chemical hazards
Each of these individuals will likely require special evacuation procedures. Train your emergency managers to handle them and provide them with the proper tools to monitor these individuals’ safety.
6. Allowing evacuation routes to become outdated
It is easy for your floor plans to change unexpectedly. For example, something as simple as a new cabinet in the hallway might cause a bottleneck during evacuations. During your evacuation drills, ask your emergency managers to monitor traffic flow and note whether new obstacles or construction have impacted your evacuation routes.
As a best practice, you want more than one evacuation route out of your facility, but that might not always be possible at smaller venues. Regardless, all of your designated fire exits should always be clear of clutter or obstacles. Checking their clearance should be a day-to-day task for everyone.
7. Not updating your EAP for new risks
Much like you need to review and update your evacuation routes periodically, you should periodically conduct risk assessments so you can understand new risks in your workplace. There are many ways you can perform these assessments. Guidance is available from each of the three national agencies linked above—the Ready Campaign from the US government in particular outlines a straightforward method for risk assessment.
8. Neglecting employee safety once they leave the premises
Identify muster points where you want your employees to assemble once they’ve successfully evacuated your building. Select muster points that are large enough to accommodate everyone.
Factor in extra capacity, as, despite your best planning, employees may not take expected routes during an evacuation and end up at different ends of the building. In addition, muster points should be far enough from your facility that assembled employees are not in danger of falling debris, smoke, or heat.
Train your emergency managers to conduct roll calls at those muster points. Roll calls help confirm who is safe and who might still be at risk. Emergency managers should be ready to share this information with emergency services as soon as possible.
Enhance Your Workplace Safety Program with Safety Technology
Emergency evacuations will be frantic, even in the best possible scenarios. Consider whether using automated workplace safety systems might simplify your evacuations and drilling.
For example, an emergency mustering system can automatically track the location of at-risk individuals in your building. Then, as employees reach muster points, the system can automatically log them safe in a digital roll call. With this support, your emergency managers can focus on first aid and coordinating with emergency service teams instead of ticking off names on a sheet.
Prepare Today, and You’ll Protect Your Company for Years to Come
A small amount of preparation and investment today will pay off for years down the road. Emergency mustering systems help streamline your workplace safety programs, make your emergency managers’ jobs more straightforward, keep all of your employees safer, and protect the financial future of your business.
Ready to see whether an emergency mustering system
is the right choice for your company?
Subscribe to our blog
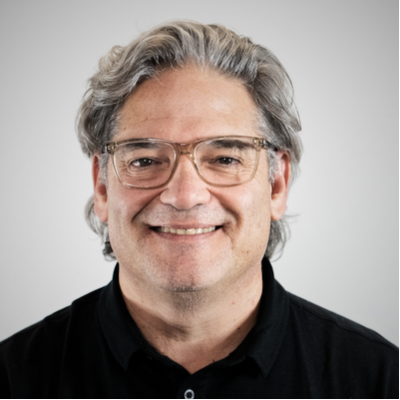
Jay Palter
Vice President of Marketing & Partnerships