By Jay Palter | July 14, 2022
When people and work assets are disconnected, your business operations suffer. So you need to keep everyone and everything streamlined and working together if you want to foster growth.
Table of Contents
The Covid pandemic blew apart traditional modes of working. Tried and true methods for connecting people and assets don’t work in hybrid or distributed working models. But major shifts were already underway before the pandemic struck. Specifically, smart and IoT technologies were disrupting the workplace.
Business leaders who want to foster growth must find new approaches to connect people and assets. This article discusses some of the steps you can take and some of the tools you can use to bring those critical business resources together.
Want to Connect People and Assets? Focus on Process
Think about how those resources are connected in your day-to-day operations. They don’t come together in a vacuum. Usually, people and assets need to connect as part of set business processes.
Technology can be an important connector of your people and assets, but you need to focus on more than just technology. If you focus on improving processes, you’ll bring your people and assets together in more efficient ways. Here are three methods you can use to help connect people and assets.
It is important to note that none of these methods are quick fixes. Quick fixes for complex business operations don’t exist. But taking time to foster these connections is an upfront investment that will pay huge dividends months and years down the road.
.
Foster a culture of learning and continuous improvement
If you’re standing still, you’re falling behind. Your competitors and customers won’t wait for you to improve. They’re looking to move forward with or without you.
For a business to improve, its employees must become more knowledgeable and capable. They need to understand how to work most efficiently with their available tools and assets. That requires continuous learning and improvement.
Unfortunately, many employees aren’t going to seek out self-improvement on their own without leadership. So you need to drive learning initiatives top-down. You need to foster a culture of learning and continuous improvement.
Lead by example and attend the same training sessions as employees. Learn about the latest tools and smart technologies in use in your organization. Build work programs to reward employees who identify any meaningful change in operations.
You can use anything from ad hoc programs to more rigorous business methodologies like Lean Management. Experiment and figure out what works best for your organization.
Share how asset use connects to strategic goals
People want to feel like they’re a part of something greater, but that doesn’t mean they want to feel like a cog in a machine—purpose matters.
Help your employees understand how their work connects to the business’s overall goals and the community within which they work. You can connect even something small, such as how employees use handheld scanners in a warehouse, to the business’s mission. Maybe your flagship product helps save lives, or it may bring joy to people all over the country. Getting those products shipped quickly and efficiently drives your company’s success and improves your customers’ lives. That is something your employees can connect to.
Use smart technology to foster deep connections between people and processes
Smart tech can facilitate deep connections to business processes that traditional equipment simply cannot match. Upgrading your equipment and infrastructure using smart technology can enable your workforce to do their job better and faster. As business becomes increasingly digital, upgrading to smart technology can help you pull ahead of competitors and find key strategic advantages in your operations.
How can smart tech do that? Let us explore this in more detail.
Learn more about Asset Tracking Solutions from Real Time Networks.
Learn MoreThe Role of Smart Tech in Business
A smart system is any business infrastructure with a built-in computer or sensor network. That network monitors the system’s performance and often performs its own analyses and modifications.
Smart technology is no longer a revolutionary concept in business. On the contrary, it is already making real, practical changes to how organizations large and small operate. Everywhere from shipping and logistics to transportation, higher education, and emergency services.
Much of the fanfare around the Internet of Things (IoT) and other smart technologies has been about its ability to connect devices for better, more automated data collection and analysis. But, as we’ve suggested here, we think a better way to think about smart technology is as a means of connecting people and business processes.
Many types of smart tech can fill this role. Typically, they’re systems that sit at the intersection of organizational and individual control of stored assets—for example, smart lockers.
Sensors Make Lockers Smart
A smart locker’s primary purposes are to improve asset management and security. It uses sensors and access controls to monitor stored assets and the personnel who want to use them.
Conventional storage lockers typically use simple access controls, such as a key, combination lock, or PIN code. Unfortunately, those methods offer little insight into who uses assets and when. On the other hand, a smart locker authenticates users with advanced digital access controls like biometrics, smartphone credentials, or RFID tokens. Those enable better device monitoring as well as detailed asset use tracking.
Lifecycle asset tracking
Business operations, threats to our businesses, and the tools to combat those threats exist in a converged reality where physical and network-based tasks are tightly integrated. As a result, we can no longer treat physical and IT security as two separate domains. In our physical security planning and implementation, we need to face security convergence head on, as these two security domains will only become increasingly aligned as time goes on.
Increased productivity
Smart lockers automate the administrative work of managing a large volume of physical business assets. Locker systems automatically track every transaction, report anomalies, and manage maintenance schedules. This smart automation allows your connected people to focus on more productive revenue-generating activities.
A smart locker system utilizes a few core components to provide these capabilities.
Smart Locker Core Components
RFID tags
Radiofrequency identification (RFID) tags are one of the most common and effective digital tagging systems. RFID is a popular short-range wireless standard. RFID tags come as either active, battery-powered, or passive-powered tags. The latter are smaller, solid-state electronics that draw remote power when they’re close to scanners.
Sensors on a smart locker access control panel scan tags when a user signs equipment in or out. You can also place a network of sensors throughout your facility that tracks equipment locations in real time for even more location and usage data.
One important benefit of passive RFID tags is that you can easily attach them to any equipment to make it location-aware. In other words, you can turn any equipment, even a complete toolkit, into a piece of smart technology when it connects to your locker system.
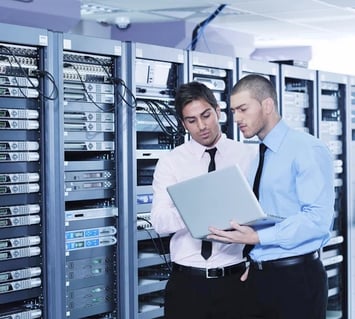
Content surveillance
Content surveillance is the name for sensors embedded inside smart locker compartments. They can verify whether a user returns the correct asset when they sign equipment back in. Content surveillance sensors can be RFID, wired USB connections, or other sensor systems. Since RFID signals can pass through hard plastic cases, you can even tag individual kit components and scan them all at once when someone signs out or returns a kit.
You can also use wired USB connections to monitor supported electronic devices. USB connections charge devices and provide a data connection between the stored electronic device and your smart locker’s central management system so you can monitor device statuses.
The term “content surveillance” covers a broad range of different sensing technologies. Smart lockers can include many specialized surveillance systems. For example, many law enforcement agencies must track pepper spray use for regulatory compliance. As a result, they often like to provision their smart lockers with scales that verify spray canister use by weight. Smart locker scales can automatically perform a weight check on canisters at signout and return to determine whether they were discharged.
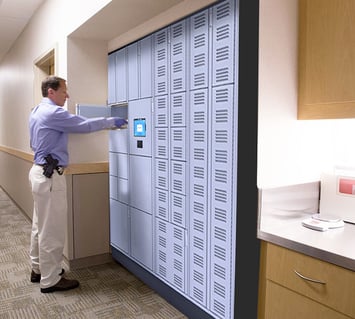
Access panels
Smart locker access control panels can present checklists to users when they sign out or return stored assets. You can use these checklists to monitor employee performance and any technical issues with stored equipment. For example, you can require employees to log any damage or error codes they encounter while using the equipment.
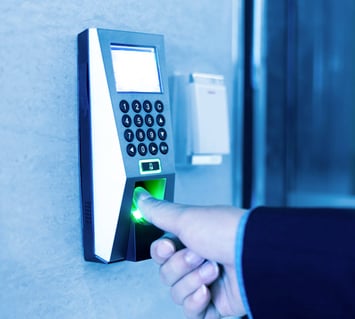
Tying it all together
Data from all of a smart locker’s sensors feed back into a central management dashboard. This dashboard is accessible through a secure web connection from any authorized PC or mobile. Administrators can use smart locker management software to monitor performance in real-time, manage users, manage assets, and generate reports for business or compliance needs.
Using a combination of all of a locker’s smart systems, you can support some very useful workflows. For example, you can control which compartments unlock in very specific circumstances. To take our warehouse working environment example from earlier in the article, if a user reports that a handheld scanner is malfunctioning in their return checklist, you can have the locker automatically lock that scanner in and prevent other users from signing it out. The system can then automatically contact your technical support team through email, notifying them of the problem.
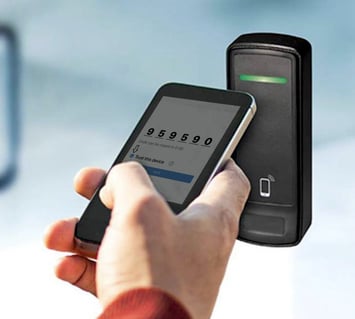
Schedule a free consultation with
a Smart Tech expert
Subscribe to our blog
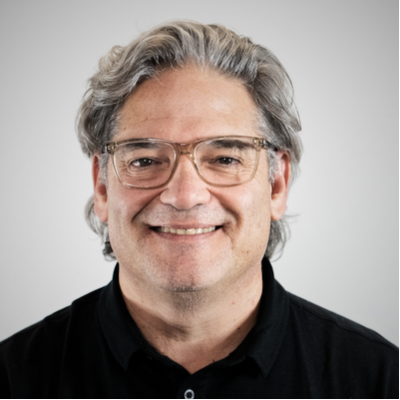
Jay Palter
Vice President of Marketing & Partnerships