By Jay Palter | May 6, 2021
There’s a reason that we call our asset lockers ‘smart lockers’. When people think ‘asset locker’ they often just envision storage space. But they can be much more.
A wide range of applications are possible building on this core set of equipment and software. Our clients have found that they can build whole new pharmaceutical inventory controls, IT troubleshooting aids, even compliance management tools.
Let’s see how.
Smart Locker Core Components...
When you boil it down, smart locker systems are made of four key components:
The Lockers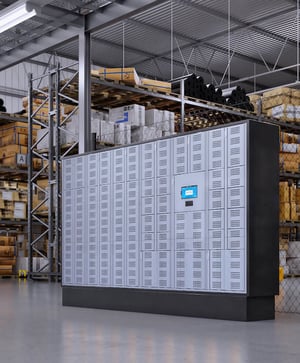
These are the secure storage spaces. They can be one-size-fits-all or stackable, modular systems like Real Time Networks deploys. Modular ones come in different sizes, which can hold assets like smartphones, laptops, evidence kits, up to long guns.
But they’re more than bare metal. They can include power and data ports for those electronics. Or digital scales for weight checks. We’ve even helped design refrigerated locker compartments to store sensitive pharmaceuticals and forensic evidence kits.
Touch Screen Terminal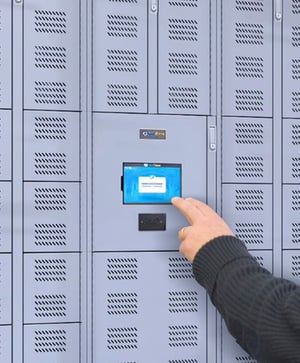
Connected to the lockers is a touchscreen panel where staff sign their assets in or out. The panels can use a range of authentication methods, including PIN code, RFID fob, swipe card, or biometrics, including, fingerprints, facial scanning, or even iris scanning.
This is where the ‘smart’ in smart lockers comes in. Some locker systems, like our AssetTracer line, allow you to implement different sign out options based on business needs. If your lockers have charging ports, you can set the terminal to only unlock the tablets or radios at full charge. Or you can establish First In, First Out rotation plans. The radio or laptop that’s at the longest—the first in—will be the first one signed out, to distribute usage and wear.
RFID Tags
As we’ll see further on, a whole range of interesting content surveillance applications open up when wireless readable RFID tags are embedded in your assets. RFID is a short range wireless communication standard that’s perfect for machine-to-machine transactions, like a smart locker verifying an asset placed inside it. RFID tags can be on keychains, embedded in durable fobs, or embedded right in things like radios, in rifle stocks, or inside laptops.
Management Software
This last piece ties everything together.
This is a central application that monitors and reports on everything that happens with your smart locker system. Real Time Networks’ system is RTNHub. It automatically compiles a transaction log and records status changes to materials in your lockers, and issues alerts and reports.
Learn how to use mobile device asset tracking technology to
The Surprising Versatility of Smart Asset Lockers
We knew many things were going to be possible using our new AssetTracer smart locker system, but even we were surprised by some of our customers’ ideas. Here are some of the more interesting problems we’ve solved so far using AssetTracer systems.
1. Airplane Safety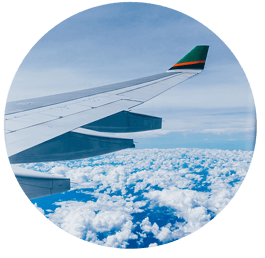
Airlines conduct their food preparation in secure airport facilities with direct access to their airplanes. Food prep requires having a lot of large, sharp knives on hand. We worked with a major airline to embed RFID tags right in the handles of their knives. Using an AssetTracer locker system they get live, automated confirmation that all knives are returned after use and don’t make their way onto airplanes.
2. Complex Asset Logging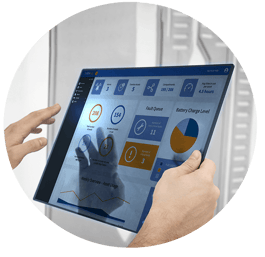
At the request of one police force we designed asset lockers that could detect the multiple different components of a radar kit inside a hardened carrying case when they’re placed inside a locker. Each piece had a tag that could transmit at high enough strength for the locker to accurately read them through the case. The RTNHub system we built for this police department reads assets individually and notifies commanding officers if any kits are returned with missing components.
3. Compliance Reporting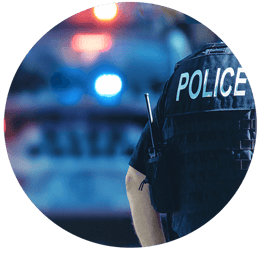
A different law enforcement agency contacted us about automating their compliance monitoring of OC (pepper) spray cans. They were required to monitor and report can weights, which tracks spray usage. We designed an AssetTracer system with scales in the lockers that would feed can weights to their RTNHub. There they could monitor cans in real time and generate customized compliance reports.
4. Customizable Workflows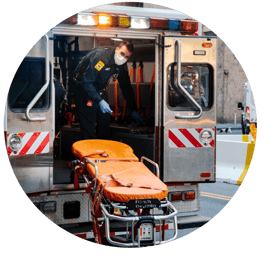
Critical materials can be managed in other ways too. A municipal EMT department needed a better way to track medications carried in their ambulances. Lives were at stake if an ambulance went on a call with low, missing, or recalled medications.
Our engineers designed a checklist application to run on their touchscreen panels when medicine bags were returned. The checklist acted as a reminder and accountability system, asking EMTs to confirm that the correct dosage amounts were in their kits when they signed out and returned bags. This checklist feature also fed updates back to their RTNHub to help them better manage ordering and recalls.
5. Laptop Repairs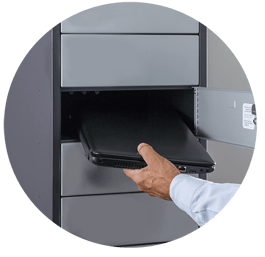
Smart lockers are individually programmable. That means different lockers can be set to trigger different alerts when items are placed in them. We’ve helped several businesses using laptops, tablets, and handheld scanners to build an inventory management system that notifies IT when an item needs troubleshooting.
In this plan, usually one or more compartments in will be designated the ‘repair lockers’ by the customer. When personnel return electronics that need repair, that person opens a case and logs notes at the panel, then deposits the item in the repair locker. This triggers a real-time alert to IT so they know a new job is waiting for them.
6. Tracking Assets Outside Lockers
We worked with a distributor who need to provision $1000 handheld scanners to warehouse personnel. These scanners were basically mobile computers with scanning guns attached. Difficult to repair and very expensive to replace. They needed the scanners secured in lockers, but they also wanted intelligence on who was using them in the warehouse, and how. We paired an AssetTracer system with wireless sensors throughout their facility that monitored device movement and usage in real-time, with tracking available through RTNHub.
This is Just the Beginning
This is just the first wave of new ideas that we’ve implemented using the AssetTracer line. As software and sensor technology advances, even tighter integration with security and business operations will become possible.
For our part, we’re looking forward to implementing full ‘cradle to grave’ asset management with AssetTracer. Controlling and securing everything related to an asset from the time it enters an organization until it’s disposed of.
A lot’s going to happen over the next few years. We can’t wait to see what other new solutions we can develop with our customers.
Do you have a tricky asset management problem you need to solve?
Subscribe to our blog
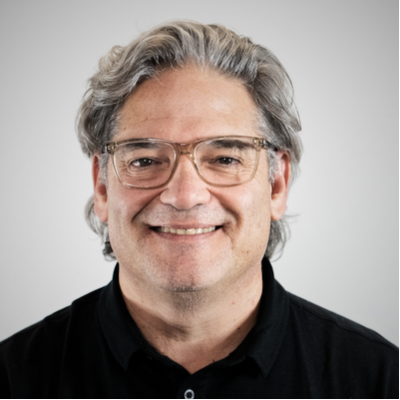
Jay Palter
Vice President of Marketing & Partnerships