By Jay Palter | August 25, 2020
How many different pieces of equipment are used by your business every day? We don’t just mean things like screwdrivers and wrenches—what about laptops? Handheld scanners? Specialized instruments?
Every business relies on a wide range of equipment to be ready and available every day, but not every business has a good way to ensure that happens. A simple, well-organized equipment inventory management plan will improve how any business purchases, tracks, and uses its equipment.
Why Improve Your Equipment Inventory Management?
Better inventory management improves day-to-day productivity, along with safety, and it saves you money. It helps ensure that your equipment is always available and in working order. Those are just some of the reasons equipment management is included as a best practice in quality control standards like ISO 9001.
When tools are ready and available at the start of their shift, your staff can get right to work. With good equipment management, you can identify and fix faulty equipment faster, which keeps your employees safe and projects on track. The usage data you collect through good inventory management also helps you make more informed purchase decisions.
Top 10 Equipment Management Best Practices
Every business has different equipment management needs, but there are some best practices every organization should work into its management programs. Here are some smart, simple things you can do to improve how your business manages its equipment:
1. Maintain a Complete Inventory
You need to be thorough. Create a master database of every valuable asset in your organization. If an item went missing and it has an appreciable impact on business performance, that item needs to be tracked.
Include all relevant information, such as serial numbers, warranty information, and department ownership. Collecting all of this can take some time, but will ultimately save you time over months and years down the road. You can expect to see more efficient management, fewer losses, and longer device lifecycles.
2. Use the Right Management Technology
Find a cost-effective equipment management system that is the right fit for your needs. Some businesses might be able to get away with using a locked cabinet and a spreadsheet inventory to manage all of their valuable equipment, but most businesses won’t.
For other businesses, the best option might be a smart locker system. These systems combine secure locker cabinets with an access control pane, and an integrated computer and sensor system. They can automate many of the administrative tasks that are part of equipment inventory management.
3. Track & Manage Usage
Good management means more than securing equipment in lockers, though. You should also track usage and damage over time. Usage tracking will help reveal where you’re over- or underutilizing equipment.
Overutilization might indicate that you need to purchase more equipment to give staff all the resources they need. Underutilization might indicate that you’ve over-purchased.
Either over- or underutilization might also indicate a performance issue in that department that you need to investigate. Why aren’t employees signing out that diagnostic laptop? Are they not bothering to run diagnostics? Or why are they signing it out so often? Are they using it for something other than diagnostics?
4. Optimize Equipment Distribution
As you collect usage data, you’ll see trends emerge in terms of under- and overutilization. Look for inefficiencies in where equipment is distributed.
Are staff making a 10-minute round trip every day across your production floor just to get a particular tool? Maybe you can set up a distribution point for those tools closer to where they start their shifts.
If you have a multisite workplace, look to see if equipment is underutilized in one location and in high demand at another. You can then redistribute equipment so it’s available where it is needed the most. Nothing collects dust. No redundant purchases need to be made.
5. Automate Procurement
Manually keeping track of replacement equipment inventories can be a challenge. We recommend building alerts into your equipment inventory management system so you’re automatically notified when you need to reorder consumables or when valuable assets near the end of their lifecycle.
If you’ve kept your inventory complete and up to date, this is easy. You can set end-of-lifecycle dates for expensive assets in your management system and schedule alerts for when those dates are approaching. If too many items are damaged and out for repair, you can have the system send an alert that inventory is low.
You can have these alerts go to department managers, or you can send them directly to purchasers. Your finance director will probably be thrilled to hear your proposal. Automation is a hot topic in finance departments right now.
Automating procurement allows much finer control over purchasing. You won’t be under-resourced, nor will you be stuck paying to store excess equipment you’ve over-purchased.
6. Monitor for Problems
Your equipment management plan needs to include a way for staff to easily report problems. Better yet, a way to automatically relay those problem reports to technicians so devices can be repaired faster.
Electronic management systems allow employees to log problems at sign-out or return through the access control terminal. We also recommend that companies managing expensive electronics designate at least one compartment as the maintenance locker in their equipment management system.
After an employee logs a device as being in need of repair, the system will prompt them to deposit the device in the maintenance locker. Technicians then receive an automated email alert with the problem report and the device’s location.
7. Implement Quality Controls
Equipment inventory systems can be customized to support other important business activities, such as improving quality controls. You can build signout and sign-in checklists into the access control terminal of some systems. These customized checklists prompt users to confirm tasks are completed.
For example, if you’re storing gauges, electronics, or other diagnostic tools, you can remind employees to check that they are calibrated. Keeping a log that verifies equipment is calibrated helps you meet ISO 9001 quality control standards.
8. Build in Maintenance Cycles
Studies have found that the costs incurred by using equipment all the way to the point of failure are 3-10 times what the ongoing costs of a good maintenance program would be. An automated equipment inventory management system can be used to rotate equipment usage so wear and tear is distributed across your entire inventory. You can keep employees from always picking the newest device off the top of the pile.
Some management systems also include a scheduling tool so users can reserve equipment. Not only does this allow employees to reserve essential items for certain jobs, but service technicians can also reserve them for preventative maintenance.
9. Prioritize Ongoing Spending
The usage data you collect will paint a picture of how equipment is used across your entire organization. You will be able to see which items are consumed the fastest, which tools break the most often, and which tools last the longest.
Learning all of that will help you prioritize future spending. You will be able to fine-tune the amount of reserve equipment you keep on hand so you’re not over- or underspending. You can buy more of the tools you use the most, and less of the items you use the least.
10. Invest in the Right Quality Equipment
When the time comes to buy replacement equipment, you can spend smarter. By applying the rest of these 10 equipment inventory best practices, you’ll know what types of equipment wear out the fastest, which brands need the least maintenance, and which tools employees want to use the most.
Is one type of essential equipment always breaking, no matter the brand? Then you know to just buy cheaper ones. Have employees learned how to best maintain another type? Then it will be cost-effective to buy higher quality equipment.
Common Sense Ideas That Provide Real Value
There are no hidden secrets to equipment inventory management. It is all about taking the time to put proven best practices into place.
Device security is important. But good equipment inventory management is about optimizing how your business buys and uses equipment over its entire lifecycle in your organization.
Learn more about securing your inventory and other valuable assets. Read our guide, Best Practices for Physical Asset Management.
Subscribe to our blog
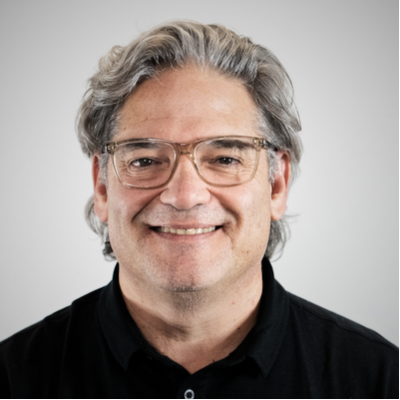
Jay Palter
Vice President of Marketing & Partnerships