By Jay Palter | August 31, 2023
Over the last decade, the pharmaceutical industry has seen overall growth, unexpected breakthroughs, sudden mergers, and just as sudden contractions. That’s before we even mention the disruptions caused by the COVID pandemic. When the market is that turbulent, businesses understandably look for reliability wherever they can find it.
They’re looking for that reliability in many areas—their customer base, product lines, manufacturing processes, and R&D. One area many should also look at is their administrative processes, specifically physical security. Security is often treated as a cost center when pharmaceutical companies should look at it as an opportunity to create operational efficiencies and even a competitive advantage by using newer, more effective smart security management technologies.
This guide explores pharmaceutical companies' physical security challenges and lays out a clear process they can follow to evaluate and deploy the most effective physical security strategy possible. It also includes use cases for how pharmaceutical companies can benefit from those new technology platforms.
What are the top physical security challenges for pharmaceutical companies?
Pharmaceutical companies face many security threats and must deploy various measures to address them. They also must navigate a complex regulatory landscape, which can make their safety and security measures even harder to maintain.
A range of security threats and safety needs
Your physical security systems play a crucial role in safeguarding your company’s production lines and offices and your intellectual property, patents, and reputation. Each faces its own unique set of constantly-evolving threats. So it's essential to establish tight control over your facility’s perimeter, keys to access resources within your facility, and often important physical assets themselves. Pharmaceutical companies must adopt a proactive, data-driven approach to their physical security.
Strict compliance and auditing standards
Meeting your compliance obligations involves navigating a complex regulatory landscape. Security breaches and even small human errors can have outsized consequences. For example, if your organization unintentionally grants the wrong person access to sensitive locations or IP. That means your security workflows should be designed to ensure absolute reliability in granting appropriate access to your facility and sensitive assets.
How can you design a reliable physical security program for a pharmaceutical company?
Comprehensive security doesn’t have to be complex security. In fact, the more streamlined, the better for most pharmaceutical businesses. Too much complexity introduces too many potential vulnerabilities. We recommend following a straightforward but comprehensive 1, 2, 3 plan to create a reliable, streamlined security program.
Conduct a risk assessment of your business
Before applying new security policies or deploying new systems, you must conduct a top-to-bottom risk assessment. Even if you think you have a fairly good understanding of your pharmaceutical company’s current risk profile, you are likely unaware of vulnerabilities or new challenges.
Pharmaceutical companies can face various potential threats, from workplace accidents, to breaches in facility security and disruptions in the supply chain. It's crucial to recognize that these risks transcend your facility's boundaries. It's important to consider both local and regional threats in addition to on-site factors. For example, whether your facility is at risk of flood, fire, or natural disasters.
Establish security protocols for your pharmaceutical company
Ensuring a safe pharmaceutical production, R&D, or administrative facility involves more than just basic perimeter defenses, like fences and locked doors. To really protect your corporate resources, you should use the information from your risk assessment to create simple, clear security protocols for everyone who works there.
The legitimate movement of your personnel can also create security risks, so it’s also important to think about how people come and go from your facility. Workers should only be authorized to access the spaces, assets, and keys they need to do their immediate jobs. For example, if someone's job doesn't require them to go to your R&D lab, they shouldn’t be able to access the physical keys for its doors.
Increased accountability for equipment use
Negligent or malicious behavior is harder to conceal when smart lockers provide precise transaction data and instant loss reporting. Take, for instance, the issue of drug diversion in EMS agencies. By attaching RFID tags to medication vials, the system can promptly alert managers when a vial is missing when EMTs return kits.
Deploy physical security management systems
At many pharmaceutical companies, security and safety measures fall to a handful of personnel carrying out manual processes. Manual security is rarely efficient and effective. Here, technology can help. Smart management systems can automatically secure your keys and assets, manage access requests, and send alerts to supervisors if something unusual happens, for example, someone requesting keys to a restricted area.
What are the use cases for smart technology management systems in pharma?
Smart key and asset management systems can help solve various problems that pharmaceutical firms face, securing their supply chain and meeting Good Manufacturing Practice (GMP) standards.
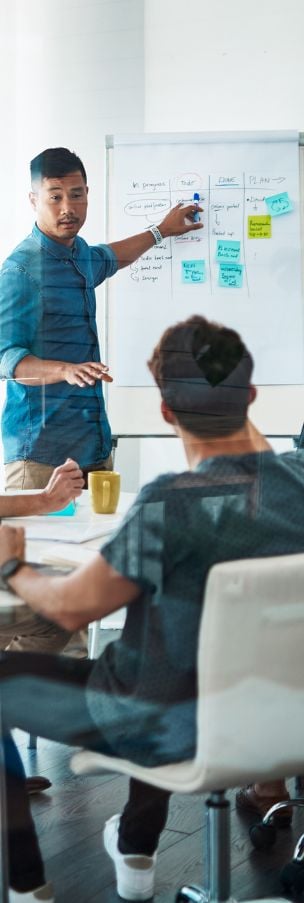
Securing high-value assets
The Problem
Pharmaceutical facilities house both valuable and regulated materials. Frozen concentrates, precursors, controlled substances. Their theft or loss is costly, especially when compounded by hefty regulatory fines.
Solution
Using an electronic key control system to manage access to your warehouse, storage rooms, or individual freezers automatically restricts access to individual keys by staff member, job type, or whatever conditions you need to set. Electronically-managed systems also help you more easily comply with comprehensive GMP physical security requirements.
You can also use a key management system to require double authentication for specific key sign-outs. For example, a Quality Lead or supervisor must enter their PIN or access card alongside a staff member signing out a freezer key. The system can also enable sign-out time limits, so supervisors receive an email alert if keys are not returned on schedule.
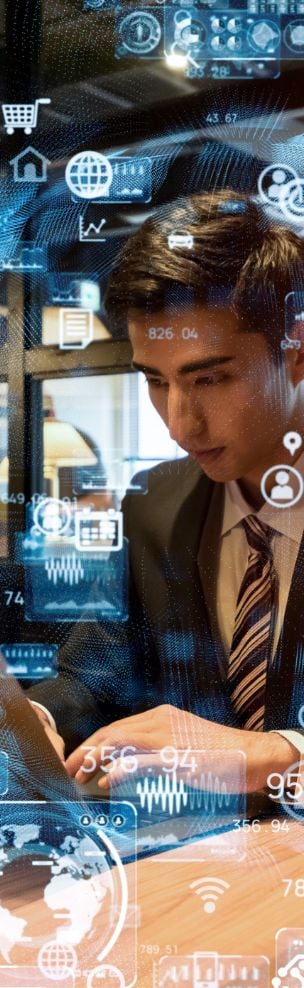
Enforcing QC quarantines
The Problem
Conducting thorough, verifiable quality control audits can be a challenge, especially in open facilities like warehouses. When materials are compromised or defective devices are pulled, you must maintain strict quarantines while audits are conducted. Without electronic key management, it can be hard to prove for regulators who had access to quarantined materials definitively.
Solution
Electronic key systems automatically compile transaction logs into reports that you can pull as needed to verify quarantines or other access controls. When you conduct particularly sensitive audits, supervisors or Quality Leads can modify access on holding cages or quarantine rooms on the fly to limit access to specific personnel or to require double authentication. You can also temporarily set certain keys to have short sign-out times to help ensure that they’re only used for essential duties in quarantined locations.
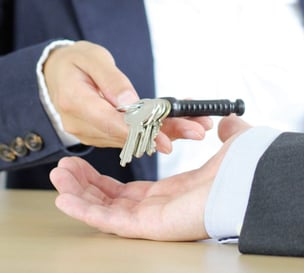
Automating routine QC task management
The Problem
You need to ensure that time-sensitive tasks are completed on schedule. This might include ambient temperature checks in freezer rooms or inventory checks in warehouses in pharma facilities. These tasks can be hard for senior QC to delegate and often remain ‘high-touch’ even when delegated.
Solution
This issue could be addressed by setting time limits on key sign-outs. The key system itself can automate some task management by notifying supervisors or Quality Leads if keys aren’t returned on schedule. Enabling double authentication for key sign-outs also helps, and letting supervisors check the system’s web app from their phone for live updates on key usage.
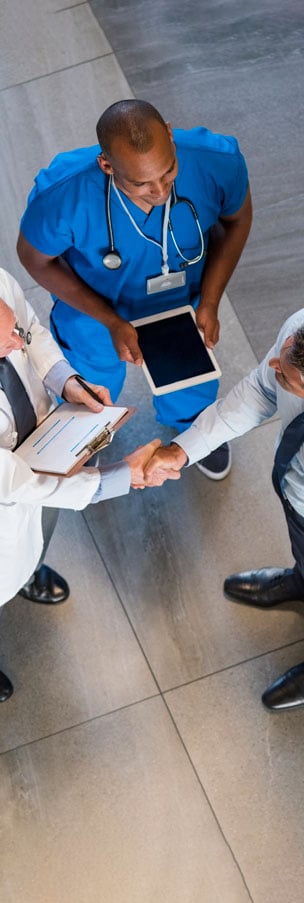
Automating reporting
The Problem
You must audit and report who can access freezers, safety cabinets, and hazardous materials. Efficiently tracking this access is challenging, especially if you’re in a multi-use facility where personnel from other departments use or pass through your space.
Solution
The transaction reports automatically compiled by electronic key systems are highly customizable. You can adapt them to your GMP audit needs or internal policy controls.
Any time limit alerts you’ve enabled on keys for sensitive assets can also be reported. These alerts can be added to your access reports to easily identify trends in employee accountability or access trends for particular assets. Are freezer checks in one portion of your warehouse consistently late? Are certain employees routinely running up against time limits? Additionally, you could utilize a smart locker system to control sensitive chemicals.
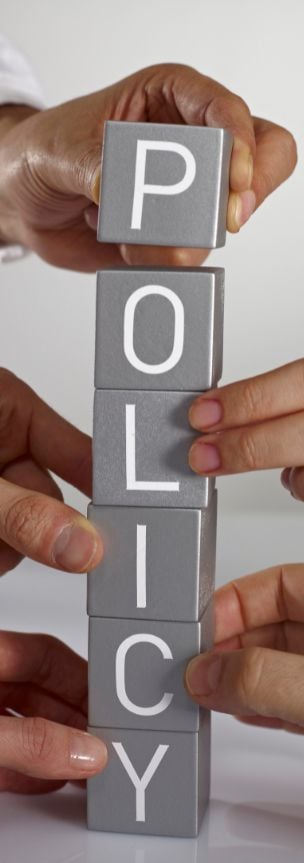
The Problem
Manually checking certifications and enforcing safety policies is time-consuming. But any accident after an employee forgets to renew a safety certification can incur hefty occupational safety violations on top of workplace injury claims.Solution
Real Time Networks’ key and fleet management systems can also control access based on certification status. For example, if an employee in your warehouse lets their forklift or scissor lift certifications expire, the system can lock them out of the vehicle key pool until they update their certs.
These key lockouts are customizable. For example, you can enable override access for emergency response teams so they can always access the vehicles or spaces they need.
Pharmaceutical businesses face a variety of challenges in securing their supply chain. There’s no magic bullet solution, but electronic key management systems can solve many of those challenges.
Contact Real Time Networks today for expert advice on designing your pharmaceutical company’s new physical security program.
Subscribe to our blog
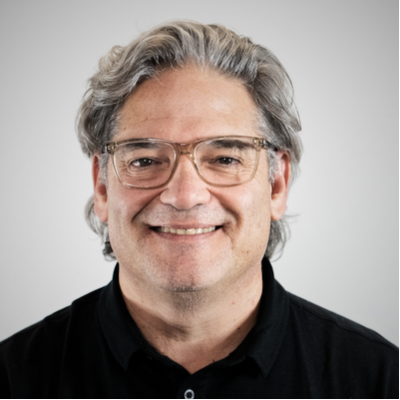
Jay Palter
Vice President of Marketing & Partnerships