By Jay Palter | April 12, 2023
Businesses large and small are looking for ways to streamline their slow, inefficient administrative tasks. And tracking business equipment is one of the most tedious and error-prone administrative tasks there is.
Equipment tracking isn’t just about preventing loss. Today's business operations depend more on mobile technology than they did even just five years ago. So if you’re missing mission-critical equipment, you may simply be unable to carry out core functions. Many organizations are investigating whether smart equipment management systems can help them automate equipment tracking cost-effectively.
In this article, we’ll explore how these systems work and why it is worth deploying equipment management systems to improve equipment tracking.
How Does an Equipment Management System Work?
Smart equipment management systems are more than the sum of their parts. They use storage and tracking tools, including modular storage lockers, wireless RFID sensors, access controls, and a smart access control panel to streamline everything about tracking equipment. Together, these components help you manage any workflow that involves stored equipment.
Let’s examine how the different components function.
Storage lockers
Smart technology still requires a reliable, real-world foundation, and in an equipment management system, that foundation consists of storage lockers. State-of-the-art lockers typically have a modular design, so you can mix and match the compartments you need to fit different equipment combinations in a limited footprint and maximize equipment safety.
That is where the simple foundation ends, though. Working its way into that bare metal and plastic foundation is a combination of smart, networked tools. For example, equipment management system lockers also typically include integrated charging and data ports to read electronic devices, ventilation, climate controls, and built-in RFID sensors to monitor sensitive devices.
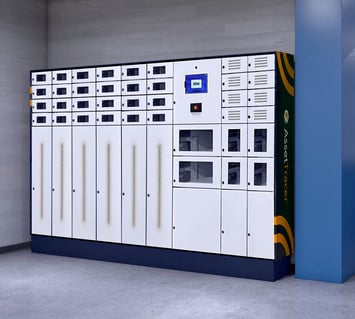
RFID tracking tags
Smart lockers include many ways to extract data about stored equipment and its use. RFID tracking tags can be active or passively powered. Active RFID tags have a built-in battery to boost their signal range and are perfect for real-time tracking of vital equipment.
Passive tags receive wireless power when they’re close to sensors. They can be manufactured smaller than a fingernail and are often embedded in devices like radios, firearms, tablets, and handheld scanners. Smart equipment management lockers typically include passive RFID sensors on their outer door so users can quickly check equipment in or out. In-compartment sensors can verify individual equipment or kit components when they’re at rest. That adds an extra layer of accountability.
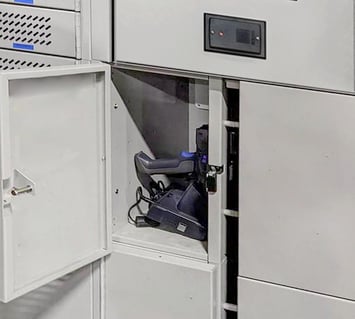
Smart terminal
Outside each equipment management locker is a touchscreen access terminal. Making access control digital provides a few important capabilities. For example, from the touchscreen, you can prompt users for additional information about their work and the equipment they’re signing out. In addition, you can specify signout curfews, present checklists, or require users to record equipment faults before returning.
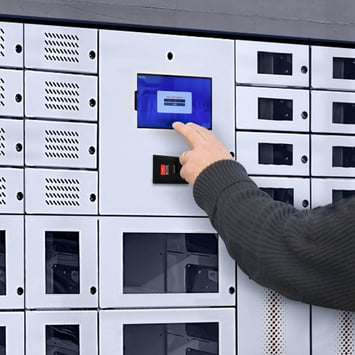
Management software
These different components are all connected by management software administrators access through a secure connection from computers or mobile devices. From the management dashboard, they can monitor locker use, change access levels, review curfew violations and other usage alerts, and generate compliance and utilization reports according to whichever criteria they need.
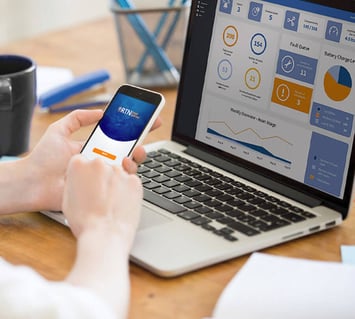
Why Use an Equipment Management System for Equipment Tracking?
For many people considering an equipment management system, it comes down to cost. They think about what it would take upfront to get the system installed. They don’t think about the labor savings. However, the latest generation of smart technology-powered equipment management systems can automate multiple tracking activities.
Automation decreases costs long term and improves efficiency
The labor savings generated by switching to automated equipment tracking quickly add up, from a few hours a week snowballing into hundreds of hours of saved labor annually. You’ll eliminate time-consuming transaction logging, tracking late returns, managing reservations, and hunting down who signed out which equipment last. Electronically-managed transactions take seconds.
And switching also eliminates costly and time-consuming human errors. Smart lockers don’t get distracted, try to work while sick, or get tired at the end of their shift. Every detail you care about is logged right the first time.
Comprehensive data collection
RFID tags and smart terminals capture far more data, and in greater detail, than human inventory managers ever could hope to collect by hand. So from the moment you add a piece of equipment to your inventory to the day you retire it, you’ll always know who used it, where it is, and if there are any problems with it. We call this ‘cradle to the grave’ tracking.
Data from RFID sensors and the access terminals collect in the central dashboard. There, you can run pore over everything in detail or look at high-level reports that summarize broad trends in equipment utilization. In addition, many users can identify usage patterns they wouldn’t otherwise notice, such as fault patterns or losses reported more frequently at certain times of the day.
You can then use that data to inform your decision-making. For example, seeing those previously-unknown fault patterns might lead you to adjust equipment maintenance schedules. Or use the equipment management system to alert technicians when devices are due for servicing and prevent regular users from signing them out.
They keep everyone accountable
Error-free recordkeeping means you always know who is using which items. So if something is overdue for return or missing at the end of a shift, you know exactly who to speak to first. By setting curfews, the equipment management system can also alert you if anything is overdue for return. So you can immediately search for equipment before it gets lost in the shuffle.
They prevent equipment losses
And, of course, they still reduce losses. The costs saved here often pale compared to streamlining business operations, but if you can avoid buying replacement handheld scanners, tablets, laptops, toolkits, or other expensive equipment, you’ll want to.
From the management dashboard, you can configure signout curfews on different pieces of equipment. Then, if an employee doesn’t return the equipment on time, your asset manager or supervisor receives an email alert prompting them to investigate. Whether it is an accident or malicious, immediately searching for missing equipment greatly increases the chance it will be found and returned.
Manage maintenance schedules
Don’t wait for your vital equipment to fail before servicing it. The best way to maintain optimal business performance is to monitor equipment for faults and stick to a reliable preventative maintenance schedule and reduce equipment downtime.
Use the checklist capabilities of your equipment management system to require users to conduct pre- and post-use equipment inspections for potential problems. For example, they can log software fault codes, mechanical problems, or cracked screens.
If someone ever reports a critical error, the equipment management system can lock the device out of circulation, preventing new users from unlocking that compartment. You can use the same alert system that notifies supervisors of an overdue return and can notify technicians that a device is ready to be picked up for servicing. They enter an override code to remove it from the locker, resolve the problem, and return it to circulation without an equipment manager needing to facilitate the process.
Equipment Management Systems Can Improve Equipment Tracking at Any Organization
An equipment management system can be an excellent addition to any company’s inventory management program. It can improve operating efficiency, reduce costs, and give you the data you need to make better decisions.
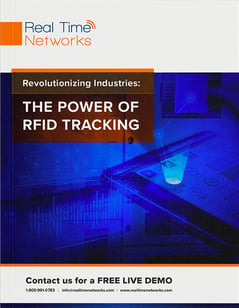
The Power of RFID Tracking
Learn how RFID tracking systems work, how to adapt them to your organization's workflows, and how they're used in various industries today.
Subscribe to our blog
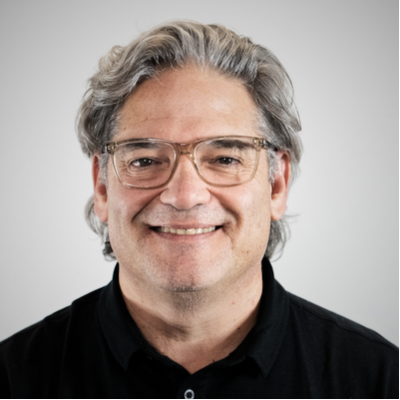
Jay Palter
Vice President of Marketing & Partnerships