By Jay Palter | August 16, 2023
Today’s volatile economy makes it difficult to plan equipment budgets. So it is no surprise that many organizations are actively seeking any new methods to make their equipment costs more predictable. Equipment lifecycle management (ELM) practices can be pivotal in streamlining your material costs and operations.
ELM enables better-informed purchasing decisions, lengthens the operational lifespan of high-value equipment, and enhances the accessibility of equipment used in critical operations.
This article explores how you can optimize your equipment lifecycle management strategy. We explain exactly how ELM works and share ten best practices organizations can adopt to improve how they use and manage their equipment.
What is an equipment lifecycle?
A piece of equipment’s lifecycle includes all information and activities from its purchase and entry into your organization to its disposal. At Realtime Networks, we use the expression “from the cradle to the grave.”
Why is systematizing equipment management so important? Wouldn’t all critical activities happen organically during use?
The core activities might happen, but business management experts have found that too many details are missed. The main benefit of ELM is optimization: purchasing optimization, usage, maintenance, and strategy. An organized ELM program extracts maximum value from equipment purchases and staff use of that equipment.
Equipment lifecycle stages
Equipment lifecycle management is typically broken out into five stages:
- Planning
- Acquisition
- Use
- Maintenance
- Disposal
In an established equipment lifecycle management program, every new purchase should pass through these five stages. If you’re starting a new program in an existing organization, you will already have a large amount of equipment in the Use stage. You’ll need to conduct an audit to gather the information you would have collected had they passed through your Planning and Acquisition stages.
Planning
The initial stage, known as the Planning stage, commences as soon as a purchasing decision is made. The process begins with investigating the various alternatives available in the market. Or, in some cases, the development of a new piece of equipment in-house.
For capital purchases, you likely want to involve stakeholders from your organization's different affected business units to provide insights on this major purchase. If you involve a wider group of decision-makers like this, you may want to conduct a use case assessment to ensure everyone has a shared understanding of the specific business problem you’re addressing with this purchase.
Acquisition
Once you have identified the asset you intend to purchase, you move on to the next stage: equipment acquisition. But why does this require a distinct stage within the equipment lifecycle?
Because acquiring new equipment involves more than just cutting a PO. In situations involving large or sensitive purchases, careful planning might be necessary to coordinate delivery, installation, training, and deployment to your facility. You also must have an established process for adding each new piece of equipment to your ELM inventory system.
Use
This is the stage of life where your employees actually use the equipment. Ideally, you want to establish a method to consistently gather and evaluate how employees use the equipment during daily operations. Typically, the most efficient approach is to use the automated tracking capabilities of a smart asset management system.
However, if you don’t have such a system already, you can still capture valuable insights through manual tracking and meticulous record-keeping. To understand their equipment performance comprehensively, consider tracking specific aspects of equipment, such as user identities, usage timings, and any reported issues.
Maintenance
Based on manufacturer guidance, set an equipment maintenance schedule for all tracked equipment and adjust for any necessary local conditions. For example, how it is used in your workplace and how often.
For larger, costlier equipment, like a forklift, consider implementing a preventive maintenance schedule, incorporating tasks like tire and battery equipment replacements. That will help lengthen their life cycles. On the other hand, a routine maintenance schedule might be more suitable for assets like handheld scanners, such as monthly software updates.
Disposal
Eventually, every piece of equipment reaches the end of its usable life cycle. The conditions for end-of-life will vary asset-to-asset, but generally, it is when the cost of maintaining a piece of equipment over a given period exceeds the utility it provides to the organization. At that point, you may have a few options, depending on the nature of a given piece of equipment.
For instance, you could recover funds by selling high-value equipment, like a retired fleet vehicle. But you’ll need to dispose of other equipment according to industry, environmental, and governmental regulations.
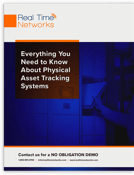
Everything You Need to Know About Physical Asset Tracking Systems
10 Equipment Lifecycle Management Best Practices
Every organization has distinct equipment management requirements, but many universal best practices exist. Here are ten useful, straightforward practices to enhance your organization's equipment management program.
Connect purchasing decisions to business strategy
“Why are we buying this?” It sounds like a rudimentary question, but too many organizations don’t actually ask this question before purchasing new equipment. Any new equipment purchase should contribute to revenue generation or expense reduction in some capacity. They should do this within your organization’s overall business strategy.
Consider whether you need the highest tier model if you need equipment that doesn’t directly further the company’s mission or increase revenue. Could you buy it refurbished? Could you delay purchasing one or two quarters? Before making any major purchase, make sure your decision-makers pause and ask, “Why are we buying this?”
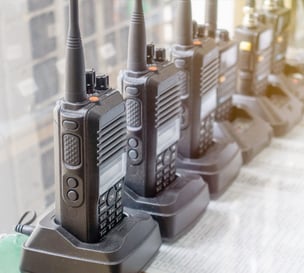
Maintain a comprehensive Inventory
Build and maintain a comprehensive master inventory of all valuable equipment within your organization. Any item that, if lost, could significantly affect business operations should be included in this inventory. Include all pertinent details, like serial numbers, warranty details, and owner.
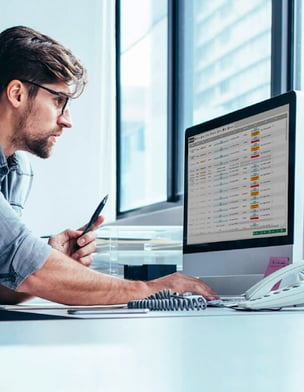
Monitor for issues
Within your equipment management program, you need a mechanism for employees to report problems easily. Even better, implement an automated system that promptly forwards these problem reports to technicians, expediting the repair process.
Smart management systems allow employees to document issues during sign-out or upon return via an easy-to-use access control terminal. Once an employee flags a device for repair, the system will guide them to place it in the designated maintenance locker. Then, technicians will receive an automated email notification with the problem description and the device's location.
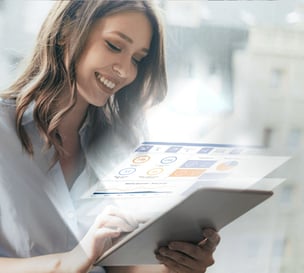
Track day-to-day equipment use
Effective management goes beyond merely securing equipment in storage lockers. It also involves equipment monitoring for usage and wear and tear. Keeping tabs on how equipment is used can uncover over- or under- equipment utilization.
Overutilization may signal a need to expand your equipment inventory to ensure your staff has all the necessary resources. Underutilization might point to unnecessary spending due to poor usage data.
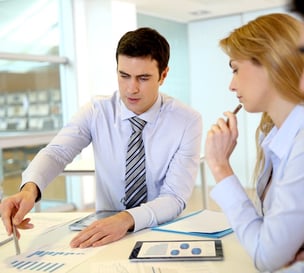
Create a procurement plan
The usage data you gather will provide a comprehensive view of how your employees use equipment throughout your entire organization. That insight will reveal which items are frequently utilized, the tools most prone to failure, and those that last the longest. This knowledge will significantly improve your budget planning. You can optimize the quantity of reserve equipment you buy, preventing excessive spending and shortages.
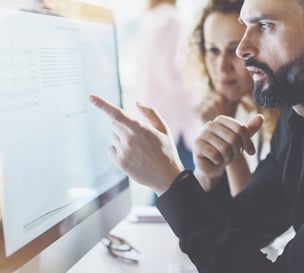
Create maintenance cycles
Research shows that the expenses incurred by running equipment until it reaches the point of failure can be 3-10 times the ongoing costs of implementing a reliable maintenance program. An automated equipment management system allows you to rotate equipment signouts, distributing wear and tear across your entire inventory. This approach prevents employees from consistently selecting their favorite device or the newest.
Optimize equipment distribution
It's crucial to identify equipment efficiencies and inefficiencies. By gathering usage data, you'll notice under and overutilization patterns. For instance, if an employee needs to make a daily 10-minute trip across the production floor just to access a specific tool, placing the distribution point closer to their time clock might be worth it.
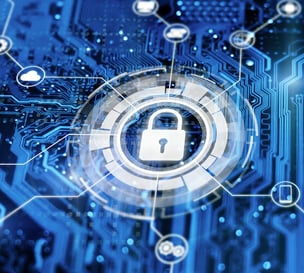
Automate procurement processes
Manually managing equipment upgrades can be challenging. We suggest integrating alerts into your equipment inventory management system that notify you when consumables need reordering or valuable assets approach the end of their lifecycle.
If your inventory is well-maintained and up-to-date, maintaining inventory levels becomes easy. These alerts can be directed to department managers or even sent directly to purchasers.
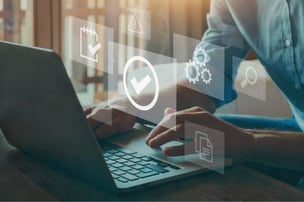
Apply quality controls
Equipment inventory systems can be customized to boost critical business functions, including your quality control measures. Within certain smart management systems, you can deploy signout and sign-in checklists directly into the access control terminal. These personalized checklists ensure users complete any necessary tasks and provide all the essential information they need for quality control.
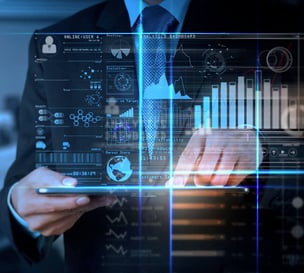
Use the right management technology
While some businesses could manage their valuable equipment with a locked cabinet and a spreadsheet inventory, more than such an approach is needed for many. A smart locker system can be the optimal choice for those other organizations. These systems seamlessly integrate secure locker cabinets with an access control panel, accompanied by an integrated computer and sensor framework. This technology platform can automate many administrative tasks, including the best practices identified here.
Smart equipment management starts a snowball of value
There are no hidden secrets to equipment inventory management. It is all about taking the time to put proven best practices into place. Each improvement makes your operations more efficient. Improving again and again over time will create a snowball effect where the value piles up. And smart equipment management systems, like AssetTracer, are some of the best platforms to create that value.
See how a smart equipment management system can help you manage your equipment lifecycles.
Subscribe to our blog
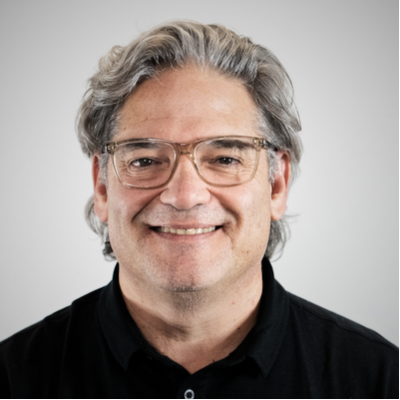
Jay Palter
Vice President of Marketing & Partnerships